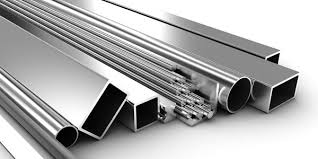
In the world of modern manufacturing, one material stands out for its combination of strength, versatility, and lightweight properties—aluminum. Used in a range of industries from aerospace to construction, aluminum has revolutionized the way we build, design, and create structures. One of the most significant developments in aluminum technology is the ability to produce large aluminum extrusion, a process that has opened new doors for engineers, architects, and manufacturers alike. These extrusions are reshaping industries, enabling the construction of stronger, more efficient, and more sustainable structures than ever before.
What Are Large Aluminum Extrusions?
Aluminum extrusion is a manufacturing process in which aluminum is forced through a die to create a specific shape. The aluminum starts as a billet, a solid piece of material that is heated until it becomes malleable. Once heated, the billet is pushed through a die under pressure, which shapes it into a desired profile. This profile can range from simple rectangular bars to complex, custom designs, and the resulting extrusions can be used for various applications.
When it comes to large aluminum extrusions, the scale of the profiles produced increases, often catering to applications where strength, size, and precision are paramount. Large aluminum extrusions are typically used in industries where heavy-duty, high-strength materials are required, and they can be customized for a wide range of applications.
Why Are Large Aluminum Extrusions Important?
Large aluminum extrusions have transformed the manufacturing world by offering a number of benefits that were previously unattainable with traditional methods. Some of the key reasons why large aluminum extrusions are so crucial in modern industries include:
1. Superior Strength and Lightweight Properties
Aluminum is renowned for its remarkable strength-to-weight ratio. In large extrusions, this characteristic is magnified. The material can bear heavy loads and withstand significant stress, making it ideal for structural applications where stability is a priority. At the same time, aluminum’s lightweight nature makes it easier to handle, transport, and assemble compared to heavier metals like steel, which would be cumbersome in large-scale applications.
In the construction industry, for example, large aluminum extrusions are often used in facades, structural beams, and supports. The strength of aluminum ensures that these components provide the necessary support for buildings, while its lightweight nature reduces the overall load and minimizes the need for additional support systems. This can result in faster, more efficient construction projects, while also lowering transportation costs.
2. Corrosion Resistance for Longevity
One of the most important advantages of aluminum, particularly in large extrusions, is its natural resistance to corrosion. Unlike other metals that may rust or deteriorate over time, aluminum forms a protective oxide layer on its surface when exposed to air. This layer prevents further corrosion, even when the material is exposed to harsh weather conditions or corrosive environments.
In industries like marine engineering, where components are exposed to saltwater and moisture, large aluminum extrusions are particularly valuable. For example, the construction of boat hulls, piers, and docks often relies on aluminum due to its corrosion resistance. In addition, architectural applications that require materials capable of enduring the elements, such as window frames, curtain walls, and cladding, often use large aluminum extrusions to provide both aesthetic appeal and long-lasting performance.
3. Design Flexibility and Customization
One of the most striking benefits of aluminum extrusion is the flexibility it offers in terms of design. The extrusion process allows manufacturers to create custom profiles that meet specific functional and aesthetic requirements. For large aluminum extrusions, this means manufacturers can produce components that are not only highly functional but also uniquely designed to meet the demands of their specific application.
For example, in the construction of commercial buildings, large aluminum extrusions can be designed to incorporate unique features such as integrated lighting channels, drainage systems, or complex architectural details. This customization enables architects and designers to explore more creative possibilities and produce components that serve multiple purposes while maintaining structural integrity.
In the automotive industry, large aluminum extrusions are often used to manufacture car frames and body components. The flexibility of the extrusion process allows manufacturers to create parts with intricate profiles that improve both performance and aesthetics. Whether it’s a lightweight frame that maximizes fuel efficiency or a strong bumper that improves safety, large aluminum extrusions help automakers meet the evolving demands of the market.
4. Cost-Effectiveness and Efficiency
The process of aluminum extrusion is highly efficient, especially when producing large quantities of components. The method allows for high-volume production with minimal waste, as the material is only used where it is needed to create the desired shape. This makes it a cost-effective solution for producing large components at scale, especially when compared to alternative manufacturing methods such as casting or forging, which may be more costly and less efficient.
For example, in the construction industry, large aluminum extrusions can be mass-produced for use in window frames, doors, and other building elements. The efficiency of the extrusion process helps reduce costs, making aluminum an attractive option for construction projects with tight budgets or large-scale needs.
Moreover, the lightweight nature of aluminum reduces transportation costs. Large aluminum extrusions are easier to move and handle than heavier materials like steel, which makes them a more economical choice for manufacturers looking to streamline their supply chain.
5. Environmental Benefits and Sustainability
As concerns about environmental sustainability continue to grow, aluminum has gained recognition as one of the most eco-friendly materials available. Unlike other metals, aluminum is highly recyclable, and it can be reused repeatedly without losing any of its properties. This makes it a valuable resource for industries that are focused on reducing their environmental impact.
Large aluminum extrusions can be made from recycled aluminum, which significantly reduces the energy required to produce the material. This not only lowers the carbon footprint of manufacturing processes but also makes aluminum an attractive option for industries seeking to adhere to green building standards or other sustainability initiatives.
In addition, the longevity of aluminum products, especially those used in construction or marine applications, contributes to sustainability. By choosing aluminum for large extrusions, manufacturers can create durable products that require less maintenance and have a longer lifespan, reducing the need for replacements and further minimizing environmental impact.
Applications of Large Aluminum Extrusions
The versatility and benefits of large aluminum extrusions have made them indispensable across a wide range of industries. Some of the most common applications of large aluminum extrusions include:
1. Construction and Architecture
Large aluminum extrusions are widely used in the construction and architecture sectors for structural components, window frames, curtain walls, and facades. Aluminum’s strength, combined with its lightweight and corrosion-resistant properties, makes it an ideal choice for buildings that must withstand the test of time and the elements. Aluminum extrusions are also used in the production of architectural details, such as columns and beams, as well as decorative elements that enhance the aesthetic appeal of buildings.
2. Aerospace and Aviation
In the aerospace industry, large aluminum extrusions are used in the construction of aircraft frames, wings, and fuselages. Aluminum’s strength-to-weight ratio is crucial for ensuring that aircraft components are both strong and lightweight, contributing to the overall performance and fuel efficiency of the aircraft. Large aluminum extrusions are also used for structural elements in spacecraft and satellites, where weight reduction is a critical factor.
3. Automotive Industry
The automotive industry has increasingly turned to large aluminum extrusions to produce car frames, bumpers, and body panels. Aluminum’s lightweight nature helps improve fuel efficiency and reduce emissions in vehicles, making it an attractive option for automakers who are striving to meet environmental regulations. Additionally, aluminum’s strength and durability make it ideal for safety-critical components, such as crash zones and structural supports.
4. Marine and Transportation
Large aluminum extrusions are commonly used in the marine industry for boat hulls, docks, and other marine components. Aluminum’s resistance to corrosion makes it an ideal material for applications exposed to saltwater and moisture. In the transportation industry, large aluminum extrusions are used for trailers, truck bodies, and other large vehicles, offering a combination of strength and lightweight properties that improve efficiency.
5. Renewable Energy
In the renewable energy sector, large aluminum extrusions are used to produce frames for solar panels and wind turbine components. Aluminum’s corrosion resistance and durability make it an excellent choice for renewable energy systems that must operate in outdoor environments, exposed to the elements. Large aluminum extrusions contribute to the overall efficiency and longevity of renewable energy installations.
Conclusion
Large aluminum extrusions have become an essential component of modern manufacturing, offering a unique combination of strength, lightweight properties, corrosion resistance, and design flexibility. These extrusions are being used across a wide range of industries, including construction, aerospace, automotive, marine, and renewable energy, to create structures that are stronger, more efficient, and more sustainable.
As industries continue to push the boundaries of innovation, large aluminum extrusions will play a pivotal role in shaping the future of manufacturing. Their versatility, cost-effectiveness, and environmental benefits make them a go-to solution for manufacturers seeking to create high-performance components and structures that meet the demands of today’s rapidly evolving markets. Whether it’s building a skyscraper, designing a new aircraft, or creating renewable energy systems, large aluminum extrusions are helping to build the future.